一、用途 熱環境混凝土工程;高爐出鐵場基礎;其它熱荷設備基礎墊層
二、特性
早強高強—— 1d 強度可達 15MPa ;
耐 高 溫——最高使用溫度可達 1200 ℃。
三、用法
開包后按比例加水機器或人工攪拌成砂漿即可澆注施工;攪拌好的砂漿應在 40min內用完。
四、貯存
50㎏/袋標準防潮包裝干燥存放3個月。
五、技術指標
型號 |
抗壓強度 MPa |
最高使用溫度 ℃ |
澆注用量㎏ /m 3 |
臨界粒度 |
1d |
28d |
600 ℃燒后 |
M-1 |
≥ 15 |
≥ 30 |
≥ 40 |
800 |
2200 |
5 ~ 15 ㎜
(粒度可調整) |
M-2 |
≥ 15 |
30 |
≥ 45 ( 1100 ℃ ) |
1200 |
2200 |
六、耐熱混凝土的定義、分類和應用 耐熱混凝土是一種能長期承受高溫作用( 200 ℃ 以上),并在高溫作用下保持所需的物理力學性能的特種混凝土。而代替耐火磚用于工業窯爐內襯的耐熱混凝土也稱為耐火混凝土。 根據所用膠結料的不同,耐熱混凝土可分為:硅酸鹽耐熱混凝土;鋁酸鹽耐熱混凝土;磷酸鹽耐熱混凝土;硫酸鹽耐熱混凝土;水玻璃耐熱混凝土;鎂質水泥耐熱混凝土;其他膠結料耐熱混凝土。 根據硬化條件可分為:水硬性耐熱混凝土;氣硬性耐熱混凝土;熱硬性耐熱混凝土。 耐熱混凝土已廣泛地用于冶金、化工、石油、輕工和建材等工業的熱工設備和長期受高溫作用的構筑物,如工業煙囪或煙道的內襯、工業窯爐的耐火內襯、高溫鍋爐的基礎及外殼。
耐熱混凝土與傳統耐火磚相比,具有下列特點: 1 、生產工藝簡單,通常僅需攪拌機和振動成型機械即可; 2 、施工簡單,并易于機械化; 3 、可以建造任何結構形式的窯爐,采用耐熱混凝土可根據生產工藝要求建造復雜的窯爐形式; 4 、耐熱混凝土窯襯整體性強,氣密性好,使用得當,可提高窯爐的使用壽命; 5 、建造窯爐的造價比耐火磚低; 6 、可充分利用工業廢渣、廢舊耐火磚以及某些地方材料和天然材料。
七、硅酸鹽耐熱混凝土 硅酸鹽耐熱混凝土所用的材料主要有硅酸鹽水泥、耐熱骨料、摻合料以及外加劑等。 1 、原材料要求 (1) 硅酸鹽水泥 可以用礦渣硅酸鹽水泥和普通硅酸鹽水泥作為其膠結材料。一般應優先選用礦渣硅酸鹽水泥,并且礦渣摻量不得大于 50 %。如選用普通硅酸鹽水泥,水泥中所摻的混合材料不得含有石灰石等易在高溫下分解和軟化或熔點較低的材料。 此外,因為水泥的耐熱性遠遠低于耐熱骨料及耐熱粉料,在保證耐熱混凝土設計強度的情況下,應盡可能減少水泥的用量,為此,要求水泥的強度等級不得低于 32.5MPa 。 用上述兩種水泥配制的耐熱混凝土最高使用溫度可以達到 700 ~ 800 ℃。其耐熱機理是:硅酸鹽水泥熟料中的 C 3 S 和 C 2 S 的水化產物 Ca(OH) 2 在高溫下脫水,生成的 CaO 與礦渣及摻合料中的活性 SiO 2 和 A1 2 O 3 又反應生成具有較強耐熱性的無水硅酸鈣和無水鋁酸鈣,使混凝土具有一定的耐熱性。
(2) 耐熱骨料 普通混凝土耐熱性不好的主要原因是一些水泥的水化產物為 Ca(OH) 2 ,水化鋁酸鈣在高溫下脫水,使水泥石結構破壞而導致混凝土碎裂;另一個原因是常用的一些骨料,如石灰石、石英砂在高溫下發生較大體積變形,還有一些骨料在高溫下發生分解,從而導致普通混凝土結構的破壞,強度降低。因此,骨料是配制耐熱混凝土一個很關鍵的因素。 常用的耐熱粗骨料有碎黏土磚、黏土熟料、碎高鋁耐火磚、礬土熟料等;細骨料有鎂砂、碎鎂質耐火磚、含 A12O3 較高的粉煤灰等。
(3) 摻合料 摻合料的作用主要有兩個:一是可增加混凝土的密實性,減少在高溫狀態下混凝土的變形;二是在用普通硅酸鹽水泥時,摻合料中的 A12O3 和 SiO 2 與水泥水化產物 Ca(OH) 2 的脫水產物 CaO 反應形成耐熱性好的無水硅酸鈣和無水鋁酸鈣,同時避免了 Ca(OH) 2 脫水引起的體積變化。所以,摻合料應選用熔點高、高溫下不變形且含有一定數量 A12O3 的材料。 目前耐熱混凝土中常用的摻合料及其技術質量要求如表 1 所示。
1 硅酸鹽耐熱混凝土常用摻合料及其技術質量要求
摻合料名稱 |
摻合料細度 (0.08mm 方孔篩篩余) |
摻合料化學成分/% |
最高使用溫度/℃ |
水泥耐熱混凝土 |
A12O3 |
SiO2 |
MgO |
CaO |
Fe2O3 |
SO3 |
燒失量 |
黏土磚粉
黏土熟料粉
高鋁磚粉
礬土熟料粉
鎂砂粉
煤磚粉
粉煤灰
礦渣粉 |
<70 %
<70 %
<70 %
<70 %
----
----
<8.5 %
<8.5 % |
≥ 30
≥ 30
≥ 65
≥ 48
≥ 70
≥ 20 |
≤ 4 |
≥ 87
≥ 87 |
≤ 5
≤ 5 |
0
≤ 5.5 |
≤ 0.3
≤ 4 |
≤ 0.5
≤ 8
≤ 5 |
≤ 900
≤ 900
1300
1300
1450
1450
1250
1250 |
硅酸鹽水泥耐熱混凝土配制時,可摻加減水劑以降低 W/C ,減少混凝土結構內部的孔隙率。減水劑宜采用非引氣型。
2 、硅酸鹽水泥耐熱混凝土的配合比 該品種耐火混凝土的配合比設計用計算法比較繁瑣,一般常采用經驗配合比為初始配合比,再通過試配調整,得到適用的配合比。表 2 為硅酸鹽水泥耐火混凝土的常用配合比,可供實際施工參考。
表 2 硅酸鹽水泥系列耐熱混凝土常用配合比 / ( kg/m 3 )
水泥 |
摻合料 |
粗骨料 |
細骨料 |
水 |
強度等級 |
最高工作度 / ℃ |
品 種 |
用量 |
品種 |
用量 |
品 種 |
用量 |
品種 |
用量 |
硅酸鹽水泥
硅酸鹽水泥
硅酸鹽水泥
礦渣水泥
普通硅酸鹽水泥 |
340
320
350
480
360 |
黏土熟料粉
紅磚
礦渣粉
粉煤灰
粉煤灰 |
300
320
300
120
200 |
碎黏土熟料
碎紅磚
碎黏土熟料
碎紅磚
碎紅磚 |
700
650
680
720
700 |
黏土熟料砂
紅磚砂
黏土熟料砂
紅磚砂
紅磚砂 |
550
580
550
600
600 |
280
270
285
285
270 |
C20
C20
C20
C20
C15 |
1100
900
1000
900
1000 |
八、鋁酸鹽水泥耐熱混凝土 鋁酸鹽水泥是一類沒有游離 CaO 的中性水泥,具有快硬、高強、熱穩定性好、耐火度高等特點。在冶金、石油化工、建材、水電和機械工業的一般窯爐上得到廣泛的應用,其使用溫度可達到 1300 ~ 1600 ℃,有的甚至能達到 1800 ℃ 左右,所以又稱為鋁酸鹽耐火混凝土。它屬于水硬性耐熱混凝土,也屬于熱硬性耐熱混凝土。
1 、膠結材 鋁酸鹽水泥耐熱混凝土的膠結材主要有礬土水泥、低鈣鋁酸鹽水泥、純鋁酸鹽水泥。
(1) 高鋁水泥 ( 普通鋁酸鹽水泥 ) 高鋁水泥是由石灰和鋁礬土按一定比例磨細后,采用燒結法和熔融法制成的一種以鋁酸 - 鈣 (CA) 為主要成分的水硬性水泥。其化學成分及礦物組成如表 3 所示。
表 3 高鋁水泥化學成分及礦物組成
類 型 |
化學成分/% |
礦物組成 |
SiO2 |
A12O3 |
CaO |
Fe2O3 |
低鐵型 A
B |
5~7
4~5 |
53~55
59~61 |
33~35
27~31 |
<2.0
<2.0 |
CA 、 C2AS
CA2 、 CA 、 C2AS |
高鐵型 A
B |
4~5
3~4 |
48~49
40~42 |
36~37
38~39 |
7~8
14~16 |
CA 、 C2AS 、 C4F
CA 、 C4AF 、 C2AS |
高鋁水泥水化的產物主要有 C 3 AH 6 、 AH 3 、 CAH 10 、 C 2 AH 8 ,而上述產物在高溫作用 下會發生脫水,脫水產物之間發生反應。如:
300 ~ 500 ℃ C3AH6 → CaO+C12A7 +H2O AH3 → A12O3 +H2O 500 ~ 1200 ℃ A12O3 +CaO → CA A12O3+C12A7 → CA( 或 CA2 ) A12O3 +CA → CA2 ( 在A12O3 較多時 )
由上可知,在 500 ℃ 以前,水泥石由高鋁水泥的水化物組成; 500 ~ 900 ℃時由水化產物及由脫水產物之間的二次反應物組成; 1000 ℃ 開始發生固相燒結; 1200 ℃ 以上時變為陶瓷結合的耐火材料。其強度的變化如圖 6 — 11 所示。
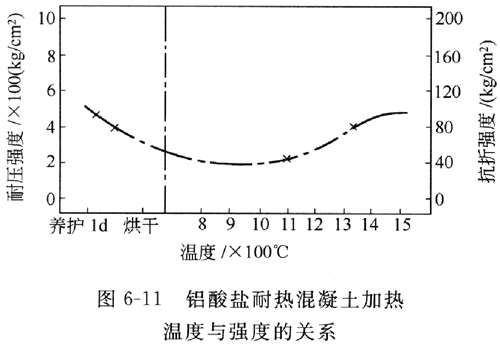
(2) 純鋁酸鹽水泥 純鋁酸鹽水泥是用工業氧化鋁和高純石灰石或方解石為原料,按一定比例混合后,采用燒結法或熔融法制成的以 CA2 或 CA 為主要礦物的水硬性水泥。其中 CA2 和 CA 含量總和在 95 %以上, CA2 占 60 %~ 65 %,另外含有少量 C12A7 和 C2AS 。 純鋁酸鹽水泥的水化硬化及在加熱過程中強度的變化與高鋁水泥類似。由于該水泥的化學組成中含有更多的 A12O3,因此在 1200 ℃ 發生燒結產生陶瓷結合后,具有更高的燒結強度和耐火度,其最高使用溫度可達 1600 ℃ 以上。
2 、骨料 由于純鋁酸鹽水泥可以配制較高溫度下工作的耐熱混凝土,因此,采用的骨料應為耐火度更高的骨料,如礬土熟料碎高鋁磚、碎鎂磚和鎂砂等。如使用溫度超過 1500 ℃ ,最好用鉻鋁渣、電熔剛玉等。
3 、摻合料 為提高耐熱混凝土的耐高溫性能,有時在配制混凝土時摻加一定量的與水泥化學成分相進的粉料,如剛玉粉、高鋁礬熟料粉等。粉料的細度一般應小于 lμm 。
九、磷酸或磷酸鹽耐熱混凝土 該耐熱混凝土是以磷酸鹽或磷酸作膠結劑和耐熱骨料等配制而成的混凝土。它是一種熱硬性耐熱混凝土。磷酸鹽耐熱混凝土使用溫度一般為 1500 ~ 1700 ℃ ,最高可達 3000 ℃ 。而磷酸鹽耐高溫混凝土可以經受 -30 ~ 2000 ℃ 的多次冷熱循環而不破壞。
1 、膠結劑
(1) 磷酸鹽 主要有鋁、鈉、鉀、鎂、銨的磷酸鹽或聚磷酸鹽,其中用得最多的是鋁、鎂和鈉的磷酸鹽。 磷酸鋁一般是磷酸二氫鋁、磷酸氫鋁和正磷酸鋁三種的混合物,其中磷酸二氫鋁的膠結性最強。使用磷酸鋁時,為加速混凝土在常溫下的硬化,可加入適量的電熔或燒結氧化鎂、氧化鈣、氧化鋅和氟化銨等作為促硬劑,也可用含有結合狀態的堿性氧化物 ( 如硅酸鹽水泥 ) 作促硬劑。 磷酸鈉鹽一般用正磷酸鈉 (Na3PO4) 、磷酸二氫鈉、聚磷酸鈉。
(2) 磷酸 磷酸有正磷酸 (H3PO4) 、焦磷酸 (H3P2O7) 及偏磷酸 (HPO3) 等,常用的主要是正磷酸。正磷酸本身無膠結性,但與耐熱骨料接觸后,會與其中的一些氧化物 ( 如氧化鎂、氧化鋁 ) 反應形成酸式磷酸鹽,從而表現出良好的膠凝性。
2 、耐火骨料 由于磷酸鹽及磷酸耐熱混凝土一般用于溫度較高的結構物中,因此其所用的耐火骨料也應選用耐火度高的材料,常用的有碎高鋁磚、鎂砂、剛玉砂等。
3 、摻合料 磷酸鹽耐熱混凝土加熱時因水分蒸發會產生較大的收縮,因此在配制時應加入一些微米級耐火材料,如剛玉粉、石英粉等。
4 、磷酸鹽耐熱混凝土的配合比 磷酸鹽耐熱混凝土的參考配合比如表 4 所示。
表 4 磷酸鹽耐熱混凝土配合比
膠結劑/% |
耐火骨料/% |
摻合料/% |
磷酸鹽溶液 |
磷酸溶液 |
耐火粉 |
碳酸鈣粉 |
18~22
---- |
----
15~20 |
70~75
73~77 |
5~7
5~7 |
2~3
2~3 |
由于磷酸鹽和磷酸對人體具有很強的腐蝕性,因此,在施工時必須注意安全,應穿好防護服、防護鞋,戴好防護手套、防護目鏡等。
十、水玻璃耐熱混凝土
水玻璃耐熱混凝土是以水玻璃為膠結料,與各種耐火骨料、粉料等按一定比例配制而成的氣硬性耐熱混凝土。它具有高溫下強度損失小、耐磨、耐腐蝕、熱震穩定性好等優點。適用溫度為 800~ 1200 ℃ ,是理想的耐火混凝土品種。
十一、耐熱混凝土的用途、材料組成及設計施工要點
普通混凝土在環境溫度超過 300 ℃ 后,其強度急劇下降,這是由于水泥石中的水化產物在高溫下分解脫水,晶格結構遭到破緣故。當溫度達到 600 ~ 900 ℃時,含有石英巖與石灰巖的集料會急劇膨脹并產生化學分解,也使混凝土強度顯著降低。所以普凝土的正常使用溫度不應超過 250 ℃ 。 耐熱混凝土是指能夠長期承受高溫 (250 ~ 1300 ℃ ) 作用高溫下保持工作所需要的物理力學性能的特種混凝土,耐熱混凝土主要用于工業窯爐基礎、外殼、煙囪及原子能壓力容器等處,長時間承受高溫作用外,還會承受加熱冷卻的反復溫度變化作。 耐熱混凝土由耐熱集料與適量的膠結料 ( 有時還添加礦物料 ) 和水按一定的比例配制而成。耐熱混凝土按其膠結材料不同為水泥耐熱混凝土和水玻璃耐熱混凝土。其中水泥耐熱混凝土又分為普通硅酸鹽水泥耐熱混凝土 ( 耐熱溫度 700 ~ 1200 ℃ ) 、礦渣酸鹽水泥耐熱混凝土 ( 耐熱溫度 700 ~ 900 ℃ ) 和高鋁水泥耐熱 ( 耐熱溫度 1300 ~ 1400 ℃ ) 等幾種。水玻璃耐熱混凝土的耐熱溫度為 600 ~ 1200 ℃。
耐熱混凝土的材料選用有如下要點。 (1) 水泥 強度等級不得低于 32.5MPa ,水泥中所摻的混合材料不得含有石灰巖類熔點低且在高溫下易于分解軟化的材料。 (2) 摻合材料 當工作溫度高于 700 ℃ 時,必須加入摻合材料。摻合材料是在拌制耐熱混凝土時摻入的具有耐熱作用的細粒粉料。加入摻合料首先可以增加混凝土的密實性,減少高溫變形;其次某些摻合料可以與水泥水化物起化學反應而減輕水泥水化物在高溫下的體積變化。摻合材料種類有黏土質 ( 黏土熟料、黏土磚、紅磚 ) 、高鋁質滴鋁磚,礬土熟料 ) 、鎂質 ( 冶金鎂砂、鎂磚 ) 、粉煤灰及高爐重礦渣等。 (3) 集料 不宜采用石灰巖及石英質集料。石灰巖集料易在高溫下分解,石英質集料在高溫下會發生較大的體積變形 ( 擴大至原體積的 1.3 ~ 1.5 倍 ) ,這些將導致混凝土結構的破壞。因此耐熱混凝土的集料應選擇在高溫下體積變形小且化學性質比較穩定的材料。可用黏土熟料、鋁礬土熟料、耐火磚碎料、紅磚碎料、高爐礦渣、碎鎂磚、燒結鎂砂、鉻鐵礦、玄武巖及輝綠巖等。集料中嚴禁混有石灰巖等有害雜質。 耐熱混凝土的配合比設計,應根據混凝土的工作強度、極限工作溫度、材料來源及經濟因素加以綜合考慮,并通過試驗確定。在試驗中應注意用水量 ( 或水玻璃用量 ) 在滿足和易性要求下應盡量減少,其坍落度應比普通混凝土小 10 ~ 20mm ;宜用機械攪拌,攪拌時間要比普通混凝土延長 1~2 分鐘。耐熱混凝土澆筑后應精心養護,水泥耐熱混凝土宜在 15 ~ 25 ℃的潮濕環境中養護,水玻璃耐熱混凝土宜在 15 ~ 30 ℃的干燥環境中養護;水泥耐熱混凝土在氣溫低于 + 7 ℃ 、水玻璃耐熱混凝土在低于 + 10 ℃ 時施工,即應按照冬期施工規定執行,并不得摻用化學促凝劑。
十二、耐火混凝土的用途、材料組成及設計施工要點 耐火混凝土是指工作于 900~ 1600 ℃ 的溫度下并保持其物理力學性能的特種混凝土,它與耐熱混凝土 有許多共同之處,在一些資料中甚至不將二者加以區分。它與耐熱混凝土的區別主要在于它往往 直接暴露于高溫火焰中,工作溫度亦更高,且較少反復加熱冷卻情況。耐火混凝土廣泛運用于冶金、石油、化工及核電等工業窯爐 中, 主要代替耐火磚用作窯爐的膛壁內襯或主體結構,它比耐火磚生產工藝簡單,施工效率高,成本低,易于滿足異形部位施工與維修,其壽命較耐火磚可提高 1 ~ 2 倍。
耐火混凝土品種繁多,其材料組成也因具體工作要求不同而多種多樣,可大致作如下分類。 (1) 按膠結材料分類 ①水硬性耐火混凝土膠結材料為硅酸鹽水泥、普通硅酸鹽水泥、礦渣硅酸鹽水泥、高鋁水泥等。它的強度形成與普通混凝土相同,都是由于水泥水化反應生成膠凝物質與集料界面緊密結合,形成具有設計強度的整體。 ②火硬性耐火混凝土 膠結材料為高鋁水泥、低鈣鋁酸鹽水泥等。火硬性耐火混凝土的膠結材料僅在混凝土澆筑成型后的一段時間由水泥水化產物產生膠凝作用,形成混凝土的初期強度,對結構本身起支持作用。當溫度升高時,在溫度 300 ~ 1200 ℃階段,混凝土內部產生一系列化學反應,水泥石由低密度水化產物轉成高密度非水化產物 ( 焙燒產物 ) ,固相體積縮小,而固體間空隙增大,混凝土強度反而降低。當繼續升溫,溫度超過 1200 ℃ 后,固相材料經燒結作用產生陶瓷結構,強度顯著提高,成為工作所需要的耐火混凝土。 ③氣硬性耐火混凝土 膠結材料為水玻璃并用氟硅酸鈉作固化劑 ( 參見耐酸堿混凝土 ) 。水玻璃耐熱混凝土粗集料常用鎂磚碎塊或黏土熟料塊,細集料常用鎂砂或黏土熟料砂,摻合料常用鎂磚粉或黏土熟料粉。
(2) 按集料成分分類 按集料成分,耐火混凝土可分為鋁質耐火混凝土主要成分為氧化鋁 (Al 2 O 3 ) ,耐火溫度 1800 ℃ 、硅質耐火混凝土主要成分為二氧化硅 (SiO 2 ) ,耐火溫度 1200 ℃ 與鎂質耐火混凝土主要成分為氧化鎂 (MgO) ,耐火溫度 800 ℃ 。
(3) 按堆密度分類 按堆密度,耐火混凝土可分為普通耐火混凝土 ( 所用集料為天然石材 ) 與輕質耐火混凝土 ( 所用集料為天然輕集料、人造輕集料及工業廢渣輕集料 ) 。
耐火混凝土的配比設計有如下要點。 ①施工條件允許的前提下,要盡可能降低水灰比,減少用水量。這是因為耐火混凝土在高溫下水分容易散失,致使混凝土孔隙增加、強度降低。 ②在滿足和易性和常溫強度的前提下,要盡可能減少膠結材料和水泥的用量。這是因為通常集料的耐火程度要高于膠結材料,高溫膠結材料先于集料發生軟化、變形。 ③加入適當的摻合材料可提高混凝土的耐火性,同時可改善和易性并減少水泥用量。常用摻合材料有黏土熟料、黏土耐火磚、黃土、礬土熟料、鎂砂、鉻鐵礦、粉煤灰、高鋁磚的磨細粉料。 ④集料要選擇適當的級配使密度達到最大,還要注意與膠結材料的匹配與適應。砂率控制在 40 %~ 60 %。配合比設計一般以經驗合比為基礎,通過試拌調整后確定。耐火混凝土一般不配鋼筋,因為鋼筋的熱膨脹系數與耐火混凝土差別很大,高溫下會導致混凝土開裂剝落,鋼筋氧化、軟化失去增強作用。必須配筋時要采取特殊措施,如鋼筋表面滲鋁抗氧化、用型鋼或埋入冷卻水管等。 耐火混凝土的施工與養護基本同耐熱混凝土。
[ 應用實例 1]
鋁酸鹽水泥耐熱混凝土在加熱爐施工中的應用
1 、鋁酸鹽水泥耐熱混凝土配合比確定 某公司烘干系統加熱爐框架結構由 4 個截面為 400mm × 500mm ,高 4000mm 的獨立柱和一個截面 400mm × 300 mm ,直徑 2500mm 的圈梁構成,設計采用極限溫度不低于 800 ℃ 的 C25 鋁酸鹽水泥耐熱混凝土。根據實際情況,混凝土采用現場攪拌的方式。
1.1 采用原材料 水泥:某水泥廠 CA — 50 鋁酸鹽水泥; 骨料:淄博 5~ 25 mm 粗焦寶石, 0~ 5 mm 細焦寶石; 外加劑:高效減水劑; 磷酸:分析純磷酸。
1.2 耐熱混凝土配合比確定及強度測試 根據設計要求對選取的耐火集料等原材料進行檢驗,并對混凝土配合比進行試配,最終確定施工配合比,如表 1 。并測試了以上配合比混凝土的各齡期抗壓強度,如表 2 。
表 1 試驗確定混凝土配合比
混凝土各材料用量 / ( kg/m 3 ) |
CA-50 |
細焦寶石 |
粗焦寶石 |
減水劑 |
磷酸 |
水 |
400 |
752 |
918 |
10.0 |
4.0 |
240 |
表 2 耐熱混凝土的各齡期抗壓強度
各齡期強度 /MPa |
1d |
3d( 110 ℃ 烘干 ) |
3d ( 800 ℃ 燒后) |
22.1 |
32.5 |
27.8 |
2 、工程應用與案例分析
2.1 事故概況
施工現場嚴格按照試驗室確定的混凝土配合比進行計量攪拌,依次對 4 個獨立柱和圈梁連續澆注,持續 10 h 澆注完畢, 7 d 后拆模板進行灑水養護。拆模板過程中,施工人員發現混凝土表面氣孔較多,且表面疏松粉化;敲擊結構,混凝土極易破碎。通過專業檢測機構對結構進行超聲波探測,發現混凝土內部產生裂紋,混凝土強度指標約為 10MPa 左右。
2.2 事故原因分析
事故發生后,從混凝土配合比設計、施工過程控制及后期養護等幾個環節展開調查。首先對此鋁酸鹽水泥耐熱混凝土的核心技術——混凝土配合比進行多次試驗和驗證,最后一致斷定此配合比完全能達到混凝土設計要求的各項性能指標。最終問題集中在混凝土的施工及養護上。據施工人員介紹,混凝土澆注施工是在六月的某天上午開始,嚴格按照混凝土施工配合比進行攪拌,由于現場攪拌能力限制,直到晚上六點才施工完畢。整個結構采用鋼模板支撐,澆注完畢 7 d 后拆除模板,進行灑水養護。
分析以上施工問題,得出以下事故原因:
a) 施工時氣溫過高。鋁酸鹽水泥水化早期集中放熱且熱量較大,當天施工氣溫在 28 -30 ℃ 之間,混凝土結構較大且采用鋼模板支模,熱量不易散失,溫度高加速水化物由亞穩定相向穩定方向轉化,使水泥石內部析出游離水增大了混凝土的孔隙率,晶體間的結合也變差,導致水泥石強度明顯 降低。
b) 早期養護不當。鋁酸鹽水泥混凝土成型后 3~6h 內應自然養護,不得給水,否則遇水能使鋁膠不斷析出而造成其不硬化,同時應防止早期失水產生碳化,而使混凝土表面疏松粉化,內部產生裂紋,嚴重影響混凝土的強度。所以水泥硬化后必須及時給水潮濕養護,使溫度控制在 15~ 25 ℃ 。施工單位在澆注 7 d 后才給水養護,導致混凝土結構因失水發生碳化,嚴重影響混凝土強度。
3 、鋁酸鹽水泥耐熱混凝土在工程施工中注意問題
鋁酸鹽水泥具有快硬、早強、耐高溫、耐腐蝕等優良性能已被廣泛應用。本文結合以上實例應用和分析,指出了鋁酸鹽水泥耐熱混凝土在工程施工中應注意的幾個問題。
a) 鋁酸鹽水泥一般不與硅酸鹽水泥、石灰等析出 Ca(OH) 2 的膠凝物混合,因為二者相混會產生閃凝,并且能生成高堿性的水化鋁酸鈣,使混凝土開裂,甚至破壞。
b) 鋁酸鹽水泥硬化時放熱量較大,且集中在早期放出,故水泥硬化開始應立即給水養護,適宜施工溫度在 15 -25 ℃ ,溫度超過 25t 時應采用降溫措施,養護期不少于 3d 。
c) 混凝土每次的拌和量應控制在 20min 內用完,拌和水應采用飲用水,期間應不斷攪拌,已硬化的混凝土不可再次給水使用,否則混凝土有可能不硬化。
d) 鋁酸鹽水泥一般不澆筑大體積混凝土,厚度不應超過 300 mm 。當用于鋼筋混凝土時,鋼筋混凝土保護層不應小于 30mm 。
[ 應用實例 2 ] 1 、普通混凝土受熱作用機理
大量研究表明,普通混凝土在高溫受熱下的退化包括質量減少,和形成大量的孔,與裂縫以及強度和彈性模量的下降,退化的結果造成普通混凝土出現大面積裂縫以至坍塌。普通混凝土受熱作用機理包括水泥水化產物受熱作用機理和水泥水化產物與骨料之間受熱相互作用機理。
1.1 水泥水化產物受熱作用機理
在火災中混凝土的溫度不斷升高,當普通混凝土被加熱到 100 ℃ 時,毛細孔開始失去水分;達到 100~ 150 ℃ 時,由于水蒸氣蒸發促進水泥逐步水化,使混凝土抗壓強度增加; 200~ 300 ℃ 時由于水泥水化產物水化硅酸鈣 凝體開始脫水而導致組織硬化; 300 ℃ 以上由于脫水加劇,混凝土收縮,開始出現裂紋,強度開始下降; 575 ℃ 時氫氧化鈣脫水,使水泥組織破壞;當溫度達到 500 、 800 ℃ 時,混凝土抗壓強度分別為原來強度的 70 %、 30 %左右,混凝土開始坍塌; 900 ℃ 時混凝土中的碳酸鈣分解,這時游離水、結晶水及水化物的脫水基本結束,混凝土強度幾乎喪失,由于氫氧化鈣的脫水,碳酸鈣的分解,混凝土中生成了氧化鈣,在射水的作用或火災后吸收空氣中的水分,氧化鈣再次水化,體積膨脹,水泥層會酥松剝落。同時,高溫改變了鈣礬石的形成機理, 600~ 800 ℃ 下鈣礬石開始水解,混凝土內部形成粗大的孔結構。
1.2 水泥石與骨料受熱作用機理
300 ℃ 時,混凝土中的骨料開始膨脹,隨著溫度的繼續升高,水泥收縮和骨料膨脹加劇,兩者結合被破壞,水泥骨架破裂成塊狀;溫度達到 500 ℃ 以上后,骨料中的石英晶體發生晶型轉變,體積膨脹,初生的不連貫裂縫迅速擴展并連續起來,形成大裂縫,造成混凝土的宏觀破壞;水泥石受拉,骨料受壓,由此加劇了內裂縫的開展,這也是強度降低的主要原因。因此,水泥用量愈大,水灰比愈大,強度降低愈大。
1.3 混凝土在火災中受損程度的影響因素
各國研究表明,混凝土在火災中受損的嚴重程度取決于以下六個因素:溫度升高的速率、最高溫度、膠凝材料和骨料的組成、水分含量及火作用的持續時間。
因此,提高混凝土的耐火性,是減少混凝土在火災中受損以至坍塌的關鍵,耐火混凝土是一種能長期承受高溫作用 ( 200 ℃ 以上 ) ,并在高溫下保持所需要的物理力學性能 ( 如有較高的耐火度、熱穩定性、荷重軟化點以及高溫下較小的收縮等 ) 的特種混凝土。該混凝土已成功地由耐火骨料 ( 粗細骨料 ) 與適量的耐火膠結料 ( 有時還有礦物摻合料或有機摻合料 ) 和水按一定比例配制而成。
2 、耐火混凝土的分類
目前對耐火混凝土的分類主要根據膠結料的不同進行分類,將耐火混凝土分為硅酸鹽耐火混凝土、鋁酸鹽耐火混凝土、磷酸鹽耐火混凝土、硫酸鹽耐火混凝土、礬土耐火混凝土、氯化物耐火混凝土、溶膠類耐火混凝土及有機物結合耐火混凝土等。
2.1 硅酸鹽耐火混凝土
以硅酸鹽做膠結料,耐火材料作骨料配制成的具有耐火性質的混凝土稱為硅酸鹽耐火混凝土。一般采用礦渣硅酸鹽水泥、普通硅酸鹽水泥或水玻璃作刀被結材料,碎粘土磚、粘土、熟料、碎高鋁磚作骨料,其最高使用溫度可以到 700~ 800 ℃ ,其耐火的主要機理是硅酸鹽水泥熟料的水化產物氫氧化鈣在高溫下 脫水,生成的氧化鈣與礦渣及摻合料中的活性氧化硅和三氧化二鋁又反應生成具有較強耐火性的無水硅酸鈣和無水鋁酸鈣,使混凝土具有一定的耐火性。如用高鋁磚、礬土熟料和碎鎂磚及鎂砂作骨料配置的耐火混凝土,最高使用溫度可達 1100 ℃ 。
2.2 鋁酸鹽耐火混凝土
以鋁酸鹽做膠結料,耐火材料作骨料配制成的具有耐火性質的混凝土稱為鋁酸鹽系列耐火混凝土。一般采用高鋁水泥和純鋁酸鈣水泥作為膠結材料。高鋁水泥是由石灰和鋁礬土按一定比例磨細后,采用燒結法和熔融法制成的—種以鋁酸鈣 (CA) 為主要成分的水硬性膠凝材料。在一系列水化反應中使水泥石由低密度水化產物轉變成高密度非水化產物,固相摩爾體積縮小,體系結構間隙增大。因此,在 1200 ℃ 以前,強度隨溫度的升高而明顯降低,到了 1200 ℃ 后,材料開始發生燒結并產生陶瓷粘結,強度提高。純鋁酸鈣水泥以下:業氧化鋁和高純石灰石或方解石為原料,按一定比例混合后,采用燒結法或熔融法制成的以二鋁酸一鈣 (CA 2 ) 或鋁酸一鈣 (CA) 為主要礦物的水硬性膠凝材料。純鋁酸鈣水泥的水化硬化及在加熱過程中強度的變化與高鋁水泥類似。由于該水泥的化學組成中含有更多的 A1 2 O 3 ,因此在 1200 ℃ 發生燒結產生陶瓷結合后,具有更高的燒結強度和耐火度,其最高使用溫度可達 1600 ℃ 以上。
2.3 磷酸鹽耐火混凝土
以磷酸鹽作結合劑,耐火材料作骨料配制成的具有耐火性質的混凝土成為磷酸鹽耐火混凝土。磷酸鹽耐火混凝土的凝結硬化與一般的水泥型耐火混凝土不同,磷酸鹽是作為結合劑而不是膠結劑,因為磷酸鹽本身在常溫下并不具有膠凝性,而是在加熱到—定溫度時,一些磷酸鹽發生分解—聚合反應,在聚合反應時,新化合物的形成和聚合具有很強的粘附作用,將骨料粘結在一起成為“混凝土”而獲得強度。常用的磷酸鋁耐火混凝土的高溫動作極限可達到 1600~ 1700 ℃ 。
2.4 硫酸鹽耐火混凝土
硫酸鹽耐火混凝土中的結合劑硫酸鹽首先水解成堿式鋁鹽 A1(SO 4 ) 3 (OH) 2 ,然后生成 Al(OH) 3 ,最后逐漸形成氫氧化鋁膠體而凝結硬化。硫酸鋁結合的耐火混凝土強度在高溫下增長較慢。溫度升至近 700 ℃ 時,強度隨溫度的提高而提高。此時,氫氧化鋁膠體大量生成并迅速形成致密的結構。硫酸鋁的化學結合水逐步脫水,由于脫水速度緩慢,對結構影響較小。
2.5 礬土耐火混凝土
礬土耐火混凝土是利用礬土水泥膠結料、耐火骨料、摻合料及水按一定比例混合成型養護和硬化而成,,礬土耐火混凝土有與耐火磚同樣的耐高溫性能 ( 最高耐火溫度 1730 ℃ ) ,與耐火磚比較,其簡化 f 制作工藝,降低了制作成本,提高了烘干爐的質量,是一種經濟性較好的耐火膠結料。
3 、耐火混凝土的研究進展
3.1 使用新型耐火膠結料
新型膠結料的開發帶來了耐火混凝土的創新。以新型低水泥耐火混凝土為例,它的結合劑 ( 高濃度陶瓷泥漿結合劑 ) 是一種綜合性系統,該系統組成中不僅包括高鋁水泥,而且還包括高分散性細粉 ( 如 SiO 2 ) 及各種無機和有機加入劑,后者為澆筑料混合物的流變學性能及工藝性能的調節劑。耐火混凝土配料組成中的高分散性組分的功能不僅保證混凝土具有較高的初始強度及密度,而且。還使混凝土在較低溫度下 (800~ 1000 ℃ ) 的強度有所提高,以及保證材料形成細的毛細管。楊笛在礬土水泥及水玻璃中加。入新型耐火粘結材料研制出—種新型鍋爐用耐火混凝土,耐火度達到 1700 ℃ 左右,可廣泛的用于電站、爐頂、爐墻、抽爐煙管道及其它耐火丁程。它具有速凝、強度增長快、方便施丁及貯存運輸等良好的可操作性能,同時還具有較高的耐火度和較好的高溫使用性能,已在衡水電廠、盤山電廠、牙克石電廠、呼市電廠等電廠得到良好的應用。莫斯科國立建筑大學開發的耐火混凝土采用新則復合硅酸鈉做結合劑,用于砌筑水泥熟料煅燒窯的燒結帶。
3.2 使用新型耐火骨料
骨料的組成是影響混凝土耐火等級的重要因素。傳統耐火混凝土常用的骨料有碎粘土磚、粘上、熟料、碎高鋁磚、碎鎂磚及鎂砂。李寶珠根據工程需要,采用了花崗巖碎石和礦渣硅酸鹽水泥,研制了耐火度達到 300~ 500 ℃ 的耐火混凝土,各項性能 指標完全滿足了設計要求。以天然輕骨料 ( 如浮石、凝灰巖等 ) 、工業廢渣輕骨料 ( 如爐渣、粉煤灰陶粒、白燃煤矸石等 ) 、人造輕骨料 ( 頁巖陶粒、粘土陶粒、膨脹珍珠巖等 ) 取代普通骨料制成的輕質混凝土,具有輕質、耐火、保溫、隔熱等優良性能。這是由于孔隙率越大的輕質混凝土,混凝土整體的熱傳導速率越低。王镕研究表明粉煤灰加氣混凝土制品是—種輕質、保溫、吸音、易加工、且耐火性能又較好的新型建筑材料。應用和推廣這種材料對減輕建筑物自重,增強建筑的保濕吸音、耐火等性能大有好處,是值得進一步推廣使用的新型建筑材料。
3.3 添加減水劑等外加劑 謝海棠通過添加復合外加劑的方法,配制出超輕高強耐火混凝土,填補了目前同內超輕耐火混凝土高溫力學強度偏低的空白。謝咸頌在混凝土配合比中摻入水泥用量 2.0 %左右的高效減水劑,拆模后耐火混凝土表面無蜂窩、露筋、孔洞等質量缺陷,經過一年多使用未見任何裂紋。工程實踐還表明,使用普通硅酸鹽水泥、火成巖骨料配制極限使用溫度不低于 800 ℃ 耐火混凝土,只要措施得當,質量完全可以保證。王廣信采用 42.5 級以上的水泥、高效減水劑和優質的細度小于 0.088mm 、含量高于 95 %的耐火骨料,經過科學計算、設計、配制成高強耐火混凝土,并將其應用在隧道窯窯車上。經三年使用效果表明其不僅能滿足耐火性能要求,抗沖擊性和抗磨損性明顯優于粘土耐火磚和普通耐火混凝土,而且維修費用低,使用壽命長。 |